Hidden toll: Exposing the real cost of inefficient CAD data exchange
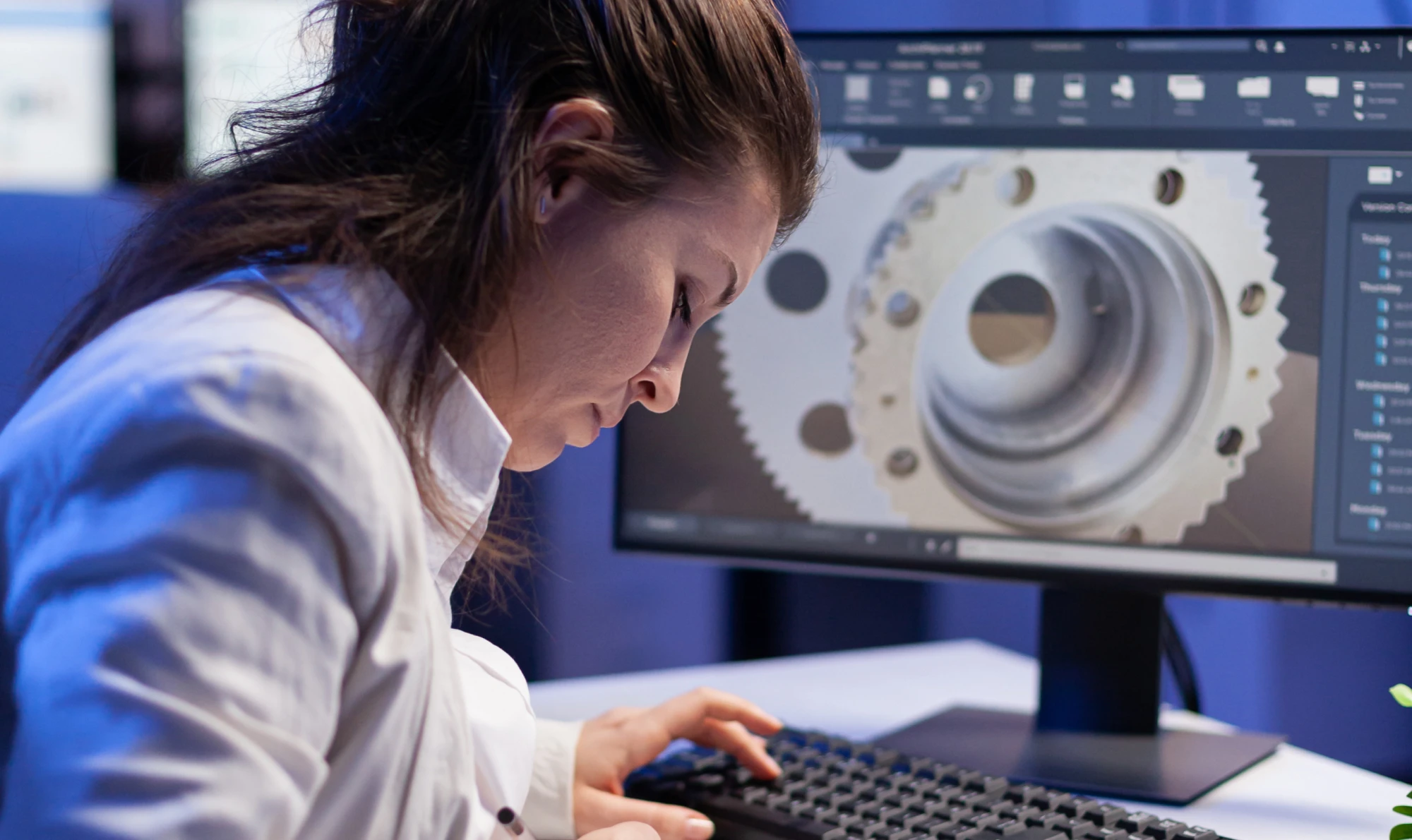
Hidden toll: Exposing the real cost of inefficient CAD data exchange
Developing modern vehicles is an increasingly complex undertaking, relying on a network of hundreds of suppliers providing thousands of individual parts, and underpinned by complex scheduling, logistics and communication requirements. But in many cases, beneath the surface, there’s a significant – and often greatly underestimated – drain on resources, time, and money. We’re talking about inefficient CAD data exchange.
If the process of sharing critical design data between OEMs and their suppliers breaks down, it can trigger a cascade of problems, leading to frustrating delays, costly errors, and substantial hidden costs that quietly chip away at profit margins. These aren't just minor inconveniences. They can potentially represent serious operational and financial challenges that hinder innovation, productivity and competitiveness.
Are these challenges impacting your projects? Take a look at our recent webinar which looks into these hidden costs in detail and explores practical strategies to overcome them: The Hidden Costs of Inefficient CAD Data Exchange
For more in-depth discussion on challenges in automotive data management, browse our schedule of upcoming webinars
Drowning in disparate systems and standards
One of the biggest hurdles facing the automotive supply chain is a lack of standardisation. Each OEM operates with its preferred CAD system (like CATIA or NX), unique data quality standards, and specific procedural requirements for data submission.
As a result, for suppliers serving multiple OEMs, the potential combinations of setups required can quickly stack up. As highlighted in our webinar, one supplier we worked with was managing up to 38 different CAD configuration setups at once just to meet the varying demands of their customer base.
This constant need to adapt, configure, and validate against different rulesets requires huge administrative effort, introduces significant potential for human error, and diverts focus from core engineering tasks.
Bleeding budgets: the impact of invisible costs
The financial impact of inefficient CAD exchange is twofold. There are the direct, visible costs: acquiring and maintaining multiple expensive CAD software licenses, paying for ongoing support, and potentially employing dedicated staff solely to manage data transfers and compliance checks.
But then there are the hidden costs, which are often far greater – the engineering hours wasted fixing or rebuilding corrupted CAD data received from a partner, the project delays due to data incompatibility, the extra cost of rework caused by design errors, and the potential financial penalties for failing to meet OEM compliance mandates. These costs add up quickly, representing a major financial burden – but one that often goes unrecognised.
Quality nightmares and version control chaos
When data exchange processes are flawed, the quality of the data also suffers. It's common for geometry or annotations to become corrupted as data is poorly translated between formats, rendering it unusable by the receiving engineer, and leading to significant delays while the data is fixed or resent.
What’s even more dangerous is the chaos that can result from poor version control. Without a clear, reliable system, teams can easily end up working on outdated CAD files. Discovering these discrepancies late in the development cycle inevitably leads to significant, expensive rework. In the worst-case scenario, if errors go undiscovered during QA, the final product's quality and integrity may be compromised, leading to serious reputational and financial damage.
Ad-hoc transfers and compliance failures
In the absence of structured, secure workflows and platforms, CAD data exchange often defaults to inefficient and risky ad-hoc methods like email attachments or generic file-sharing platforms. This creates a "file transfer limbo" where tracking data status is difficult, and commercially sensitive intellectual property is potentially exposed. This lack of process discipline also has a negative impact on change management, adding further delays whenever design updates are needed.
The reality is that, without dedicated systems and expert resources, managing complex web OEM-specific compliance rules such as data quality checks, stringent metadata requirements, and robust security protocols is extremely challenging — almost impossible in some cases.
The human factor: skills gaps, turnover, and overload
Compounding these technical and process issues is the human element. Finding and retaining personnel with the specialised skills needed to navigate multiple complex CAD systems and OEM exchange protocols is increasingly difficult. High staff turnover can exacerbate the problem, leading to a loss of critical process knowledge and inconsistency.
As noted in our webinar, the sheer volume of data being generated globally is exploding – 90% of the world's data was created in the last two years, overwhelming engineers and knowledge workers. The introduction of new technologies surrounding electric and automated vehicles only adds to this complexity, demanding new data types and straining existing skills and processes further.
Overcoming CAD data exchange challenges
Simply turning a blind eye to the inefficiencies embedded in CAD data exchange is a high-risk strategy in the hyper-competitive automotive sector. The cumulative toll – measured in wasted budgets, delayed projects, compromised quality, and strain on supply chain relationships is simply too great to ignore.
Recognising these issues within your own workflows is a crucial first step toward implementing robust solutions that streamline workflows, eliminate hidden costs, and restore efficiency to the critical OEM-supplier interface. Don't let inefficient processes undermine your success. Talk to Majenta about the cutting-edge solutions we can offer. You can get in touch via the link below.