Leveraging 4D Modelling at Southern Water
The use of 4D modelling has already resulted in substantial resource and cost savings, with further savings expected as the project enters the construction phase. The collaborative process ensured the project plan was optimised for efficiency and safety.

Customer Challenge
The Brighton East project, a collaboration between Majenta, Binnies, and Galliford Try (GTb), aimed to build a water treatment facility in the car park of Southern Water's Southern House complex.
The project's location posed significant challenges, requiring meticulous planning to minimise disruption to the client's building and operations. The team needed to optimise site setup, plan vehicle access, streamline construction schedules, and ensure the safety of workers and the public. Effective communication with Southern Water was crucial to informing all stakeholders about the project's timeline and its impact on their operations.

The Majenta Solution
Majenta provided advanced 4D modelling services to address the project's challenges. Despite common perceptions that extensive pre-existing data is required, Majenta built the models using 2D data provided by the project stakeholders.
The initial model was created from 2D drawings and refined through workshops with Binnies and Galliford Try. During the pre-construction phase, the team conducted 4D rehearsals, visualising the project being built and identifying potential issues before construction began. The model facilitated effective communication with Southern Water, optimised site setup and infrastructure placement, planned vehicle access, streamlined construction schedules, and enhanced health and safety by rerouting pedestrian walkways. The 4D model also helped plan the demolition sequence, minimising disruptions to the surrounding areas.

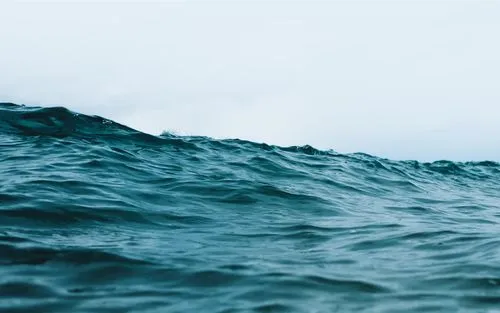
Business Impact
The use of 4D modelling has already resulted in substantial resource and cost savings, with further savings expected as the project enters the construction phase. The collaborative process ensured the project plan was optimised for efficiency and safety.
The model helped establish fence lines that could remain in place for the entire project duration, saving time and costs. It also enabled the team to re-route vehicle access, improving efficiency and safety. The 4D model allowed for the optimisation of concrete pour sequences and the formation of octagonal bases before pouring the main slab, further streamlining the construction process.
By providing clarity on the demolition sequence, the model minimised disruptions to the surrounding areas. The technology also enhanced health and safety by creating a safer environment for workers and the public. As the project progresses, stakeholders will continue to leverage the 4D model for rehearsal and analysis.