Empowering a Global Automotive Supplier with Enhanced CAD Processes
Majenta worked with the Supplier to overcome geographical and technical challenges, improve CAD processes, and enhance data management efficiency, enabling them to deliver on complex automotive projects for JLR successfully.

faster data processing time for large project volumes thanks to improved VDI performance.
reduction in skills gaps according to post-training evaluations — enhancing the Supplier's ability to manage complex CAD projects.
of JLR project deadlines met by overcoming geographical and technical constraints that had previously impacted delivery.
increase in data management efficiency due to a successful transition to a structured PLM system.
Project context
Our client — “the Supplier” — a full-service automotive supplier based in China, had been collaborating with Majenta since 2018 on various projects, including door designs for Jaguar Land Rover (JLR).
However, their geographical location presented significant challenges. A direct connection to Majenta's systems was not feasible, and their Virtual Desktop Infrastructure (VDI) performance struggled to handle the large volumes of data required for these complex projects.
Compounding the challenge, the Supplier's internal CAD processes were underdeveloped, relying on a less efficient file-based data management system rather than a structured Product Lifecycle Management (PLM) environment. High staff turnover within the Supplier's organisation also created significant skills gaps, impacting their ability to effectively manage CAD data and associated processes.

Majenta implemented a comprehensive solution to address these challenges.
Consulting on PLM integration — Majenta provided expert consulting services to support the Supplier's transition from a file-based system to a structured PLM environment.
Optimising data workflows — We developed and implemented optimised data workflows specifically designed to handle large volumes of data without needing a direct connection.
Ongoing CAD training and support — To mitigate the impact of high staff turnover, Majenta provided continuous CAD training and comprehensive support services.

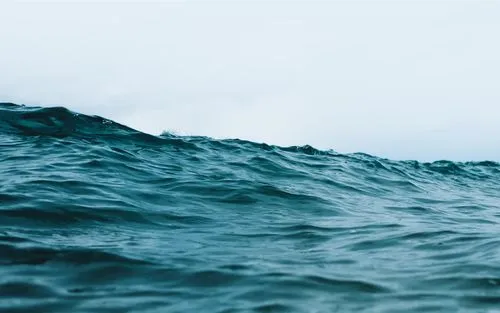
Majenta's comprehensive approach resulted in significant process and efficiency improvements for the Supplier.
The optimised data workflows enabled the Supplier to efficiently handle large datasets, even without directly connecting to Majenta’s systems. This improved efficiency ensured the Supplier could consistently meet critical JLR project deadlines despite significant geographical and technical constraints.
The smooth transition to a structured PLM system resulted in significantly better data management, reduced errors in design processes, and enhanced collaboration across teams — and the continuous training and support provided by Majenta played a crucial role in closing the skills gap within the Supplier's organisation.
This transition provided the Supplier with the essential expertise needed to manage complex CAD projects more effectively, mitigating the challenges posed by high staff turnover and ensuring a consistent level of competency within their team.
By focusing our engagement on the Supplier's specific points of weakness, Majenta empowered them to enhance their CAD processes, improve efficiency, and strengthen their relationship with key clients, including JLR.