Streamlining Data Exchange for Motherson SMR and Nissan
Majenta worked with Motherson SMR, a UK and India-based supplier of exterior mirrors, to overcome data exchange challenges with Nissan, ensuring seamless project delivery, adherence to stringent data requirements, and improved workflow efficiency.

reduction in CAD data errors as a result of introducing structured workflows.
of Nissan project milestones met without delays.
reduction in time spent processing G2B applications and PDS submissions.
accuracy in mapping part numbers to Nissan’s system, reducing manual interventions.
Impact at a glance.
With the project still in the pre-construction phase, substantial resource and cost savings have already been realised. Further savings are expected as WGM continues to leverage the 4D model for rehearsal and continuous analysis as work begins.
.webp)
Project Context
SMR faced significant challenges in providing design data to Nissan due to a lack of access to the Nissan Supplier Tool Kit (NSTK). The supplier’s internal part numbering system did not directly map to Nissan's, requiring complex part number mapping in line with Nissan's strict numbering policies. Nissan's Teamcenter system, with its unique part numbering conventions, necessitated bespoke workflows and manual intervention to manage the release of SMR's parts. Adherence to Nissan's strict modelling practices (Paperless Model) added further complexity, making NSTK (Teamcenter) installation business-critical.

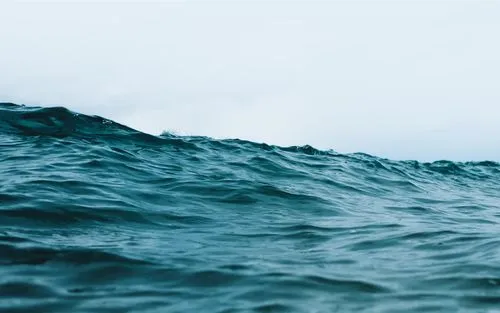
Majenta implemented a multi-faceted solution to address these challenges.
Bespoke CAD workflows
We developed bespoke CAD workflows using Excel to map SMR’s part numbers to Nissan’s system, ensuring seamless data integration and compliance.
Data enhancement
Our team updated and added CAD data PMI (Product Data Information), annotation, and PDM attributes, and performed data checks.
G2B and PDS support
On behalf of SMR, Majenta processed G2B applications, completed Spec Tender replies, and created PDS (Proposal Data Submission) forms.
Data upload to Teamcenter
We uploaded CAD data, supporting documentation (Data Note in Excel format), and TIFF formatted drawings to Teamcenter P3.
Our solution delivered substantial improvements, enabling SMR to meet Nissan's stringent requirements.
By implementing tailored solutions, Majenta enabled SMR to successfully meet all contractual obligations with Nissan, achieving a 100% success rate in meeting project milestones without costly delays.
The improved part number mapping and streamlined data management processes led to smoother, more efficient workflows throughout the product development lifecycle. This enhanced efficiency, coupled with Majenta's expert management of the data submission process, allowed SMR to focus on design and engineering, rather than administrative tasks.
Ultimately, Majenta’s solution facilitated faster project timelines and improved supplier adherence to Nissan's stringent data standards and Paperless Model requirements. The successful project solidified SMR's position as a reliable supplier to Nissan, strengthening their long-term business relationship.