Stay informed on digital engineering
Browse the latest technology updates, industry insights and engineering thinking from our in-house experts.
Thank you! Your submission has been received!
Oops! Something went wrong while submitting the form.
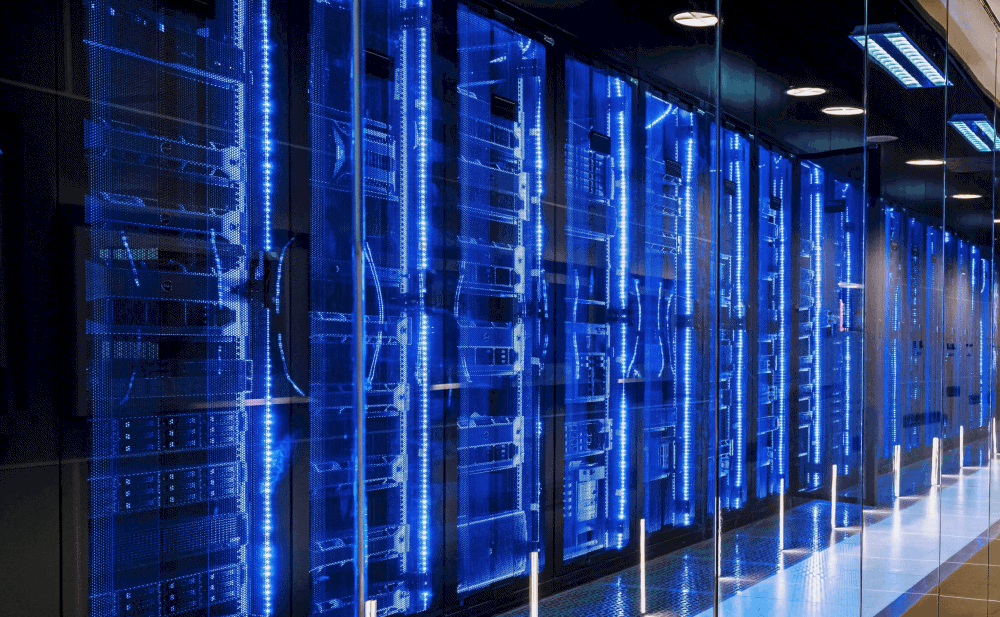
Is the UK fully prepared to capitalise on the data centre boom?
This article outlines the key challenges threatening the UK’s ambitions in the data centre market—high energy costs, power grid delays, and a slow planning system. It highlights how these barriers could stall investment unless tackled head-on. It also explains how digital construction methods like BIM, modular builds, and digital twins can help reduce costs, speed up delivery, and make the UK more competitive.
June 27, 2025
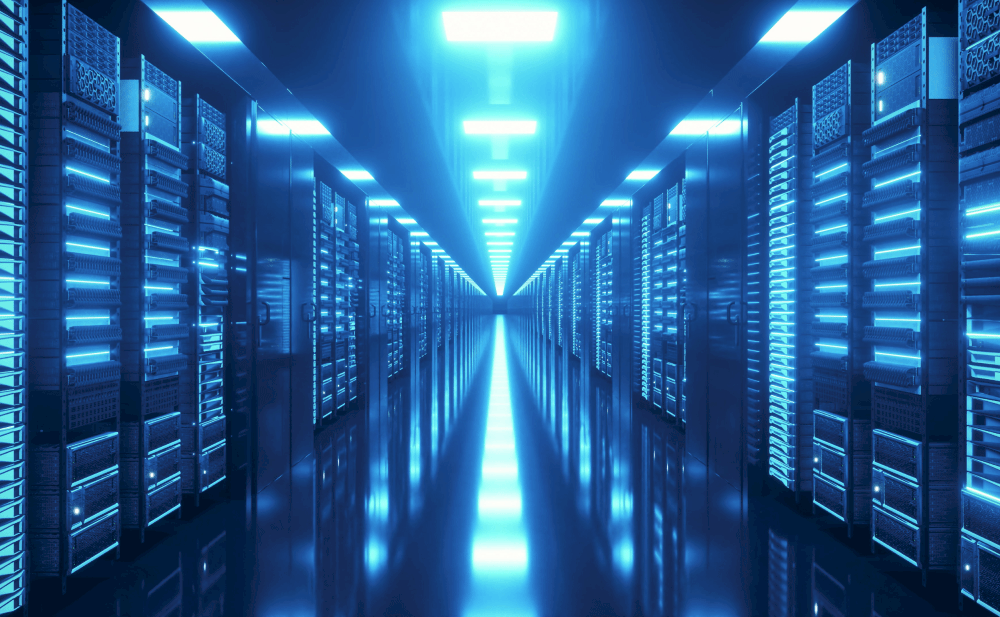
Can the UK leverage its advantages to lead the data centre race?
This article looks at how the UK can lead in the global data centre boom, driven by demand for cloud and AI. It outlines the UK’s key advantages—geographic location, regulatory stability, skilled talent, and strong transatlantic ties—and how digital construction tools can boost efficiency and sustainability. But it also warns that to stay ahead, the UK must move fast on planning, energy, and infrastructure.
June 26, 2025
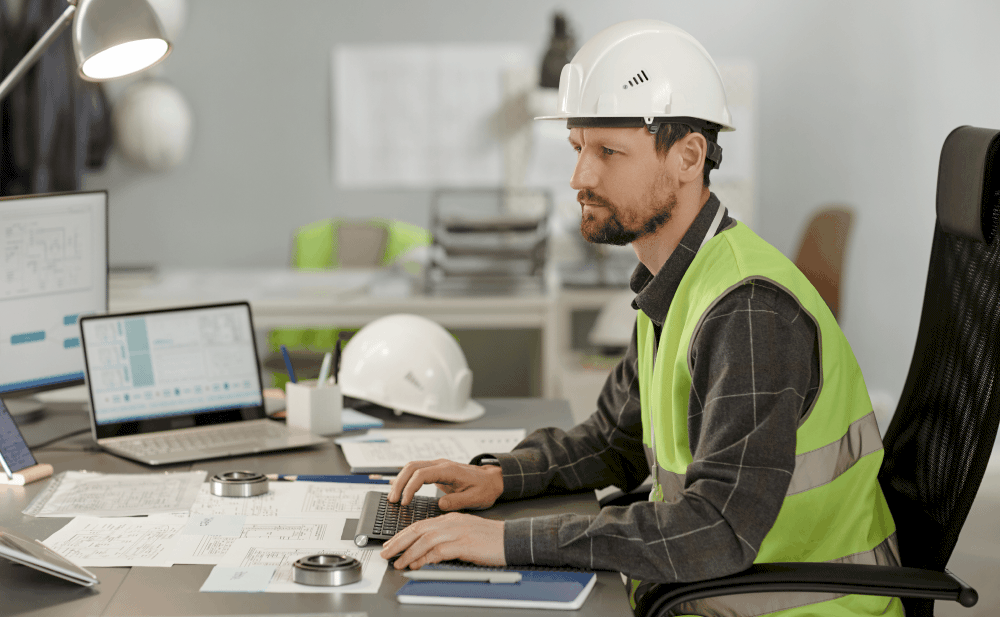
Are legacy engineering processes costing you more than you think?
This article explains how legacy engineering processes can slow down automotive firms, waste resources, and block innovation. It covers the hidden costs of outdated workflows, the risk of automation without clean data, and why AI can’t fix broken systems—it just scales the problems. It also makes the case for structured, well-integrated data as the foundation for any digital transformation effort.
June 25, 2025
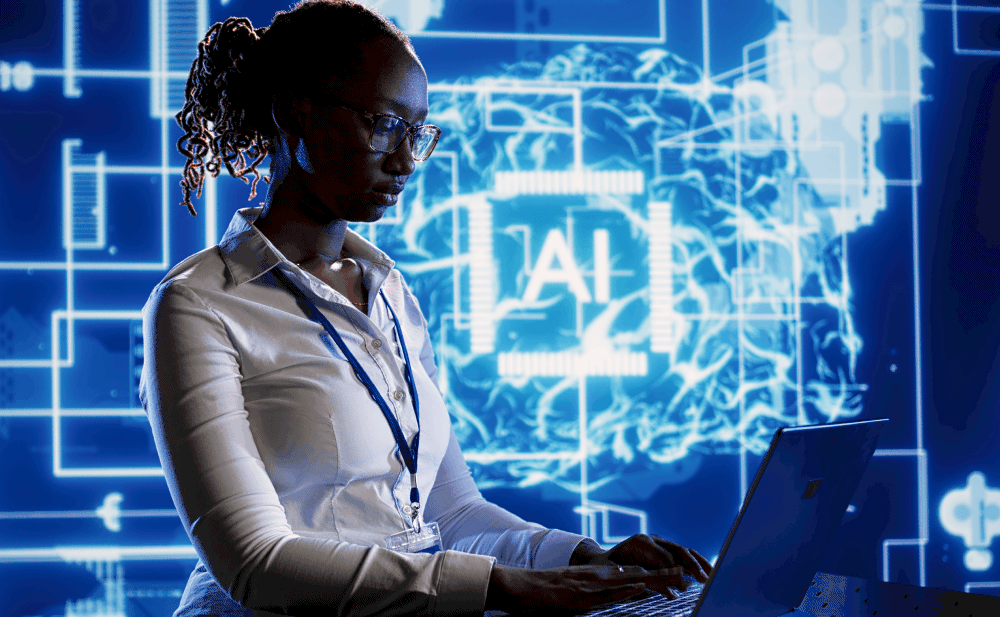
How Digital Transformation Drives Efficiency and Innovation
This article explores how digital transformation is reshaping automotive engineering. It outlines the role of smart automation in reducing manual data handling, the importance of system connectivity in breaking down data silos, and how clean, structured data lays the groundwork for effective AI use. It also highlights why external expertise is often key to managing complex data exchange challenges.
June 25, 2025
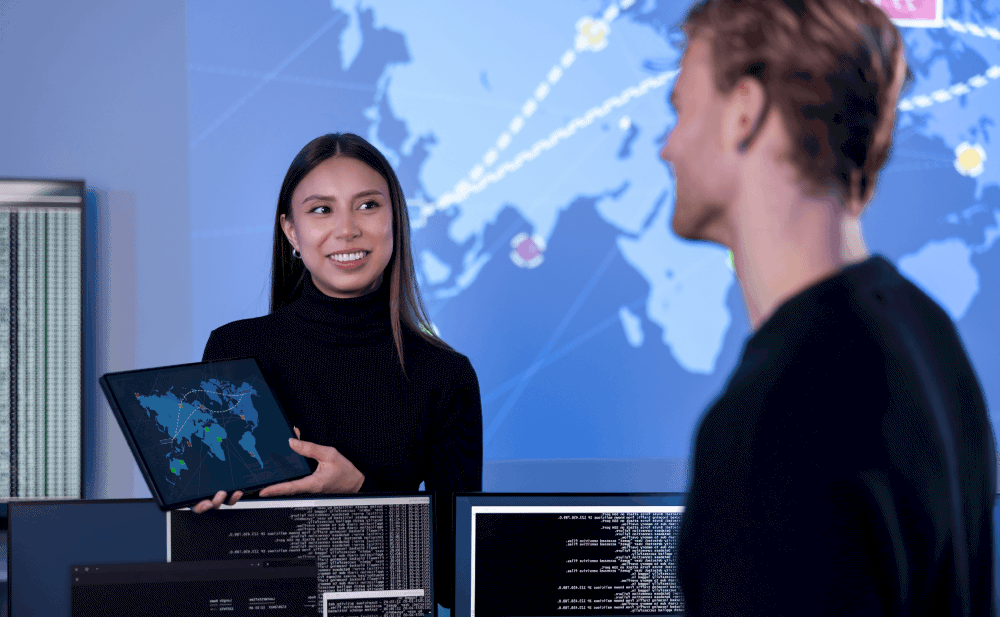
Overcoming Key Challenges in CAD Data Exchange
Given the high-stakes, fast-paced nature of modern automotive engineering, the exchange of CAD data between OEMs and their complex network of suppliers is a critical process. Missteps can lead to costly delays, frustrating errors, and strained relationships, ultimately impacting a project's bottom line and time-to-market.
June 24, 2025
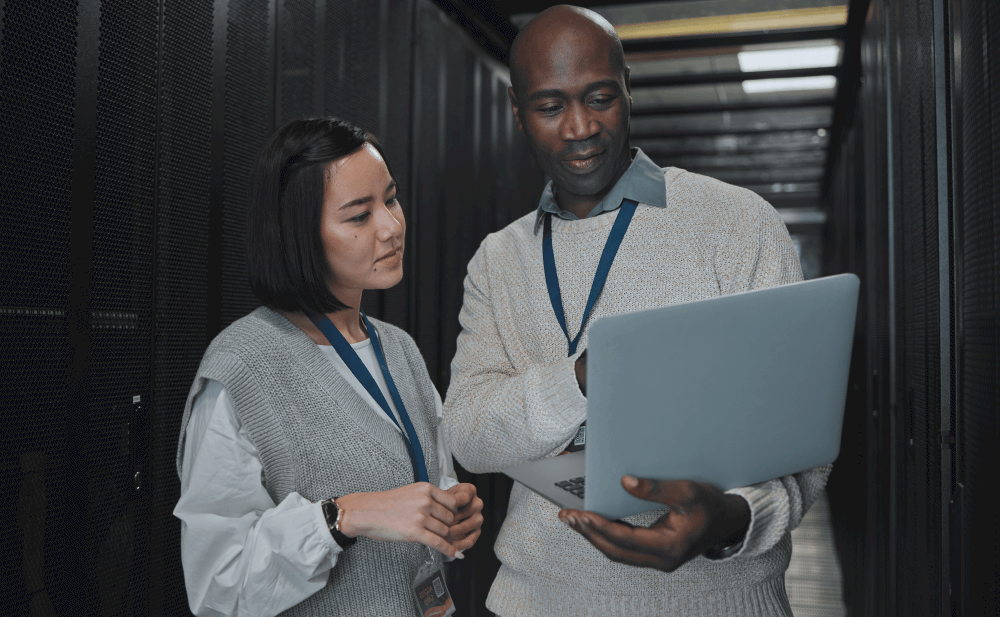
A Day in the Life of a Data Coordinator
Automotive design and manufacturing rely on complex data flowing seamlessly between OEMs and their network of suppliers: design specifications, engineering changes, and manufacturing instructions, all of which must be perfectly aligned to bring new vehicles to market on time and within budget.
June 24, 2025
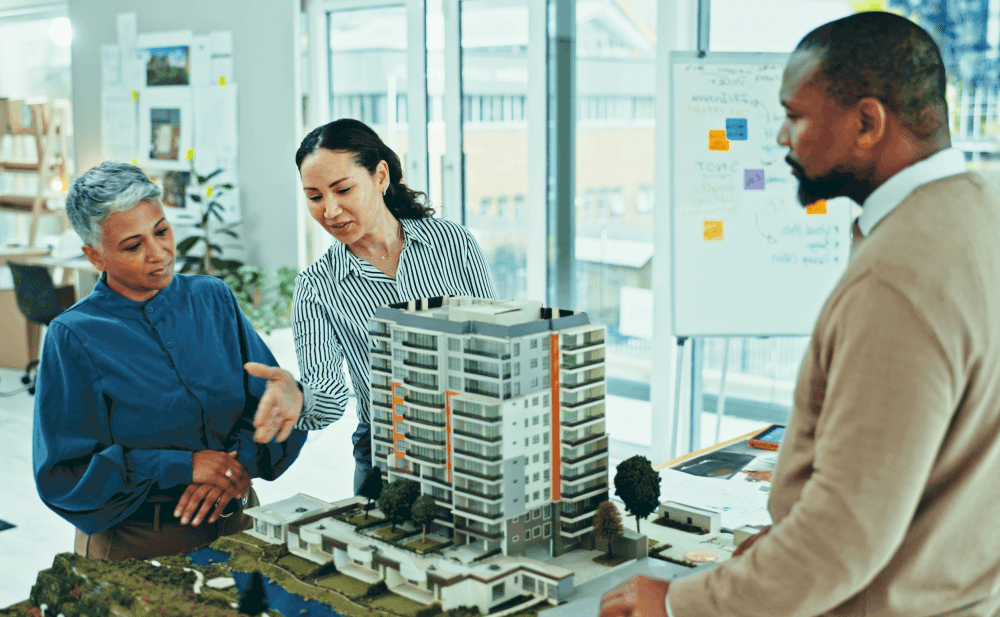
The BIM bottleneck (and how to fix it)
The potential for BIM and digital construction to create more sustainable, more efficiently run built estates is widely acknowledged, bringing streamlined processes, better data, and enhanced collaboration. But there are two persistent questions we hear from estate owners and managers. If BIM is so powerful, why do we still find ourselves facing so many information management challenges? And why aren’t we seeing the full benefits in the operational phase?
June 5, 2025
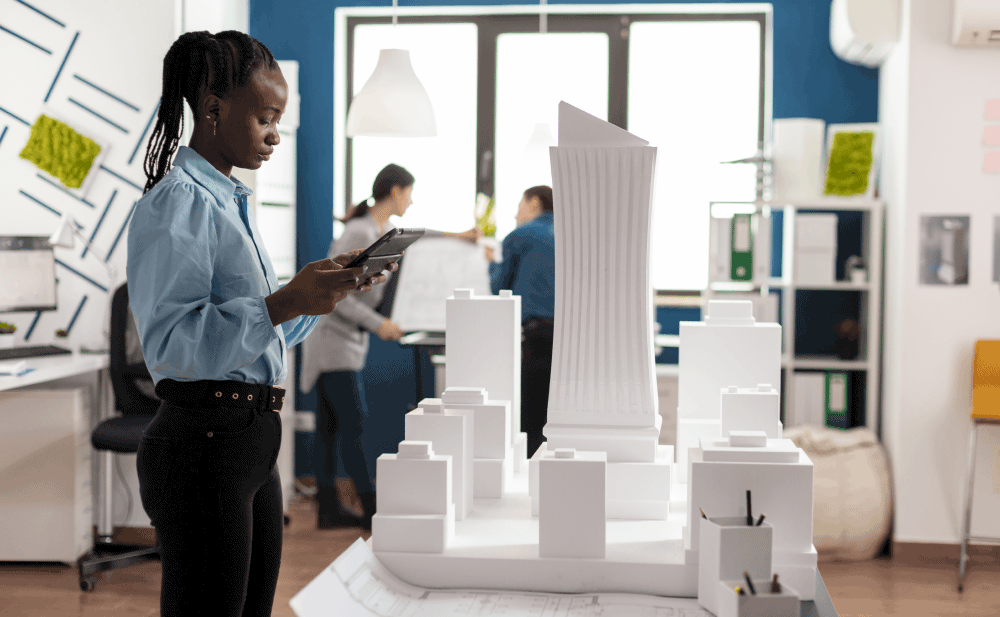
Towards a greener future: How BIM is revolutionising building management
Owners and managers of large built estates are increasingly seeking innovative solutions to a key challenge: how do we reduce our environmental footprint while simultaneously streamlining operations and ensuring our buildings are fit for the future?
June 4, 2025
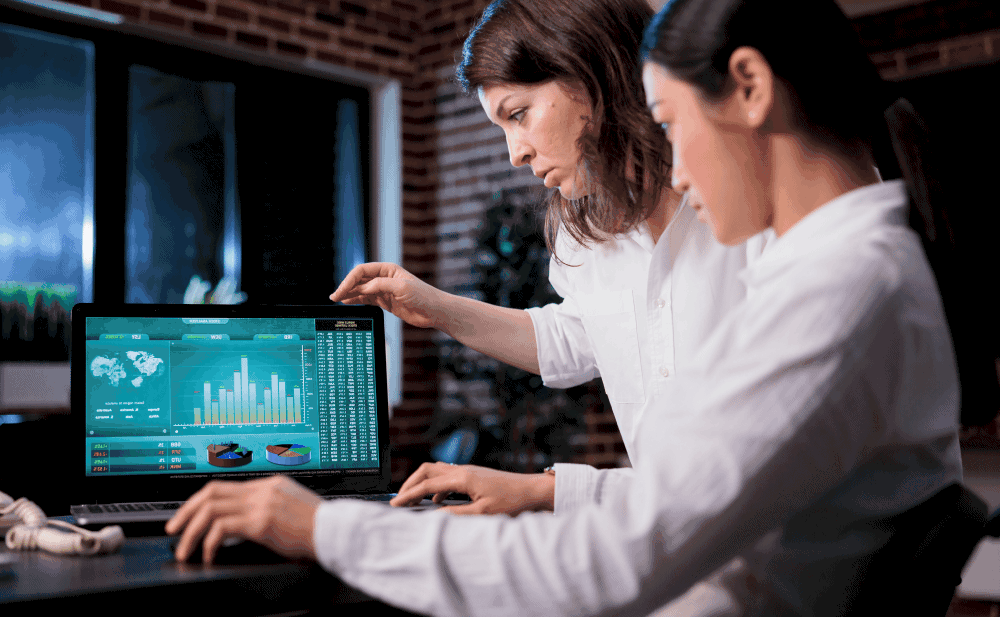
Is Your Engineering Data a Ticking Time Bomb?
In automotive engineering, designs, intellectual property, and engineering data are foundational to your ability to innovate and maintain a competitive edge. But what if the very methods you use to share this critical information are silently exposing your business to significant, potentially catastrophic threats? This post uncovers the often-overlooked dangers of outdated file-sharing practices – the ticking time bombs that could be lurking in your workflows.
May 31, 2025
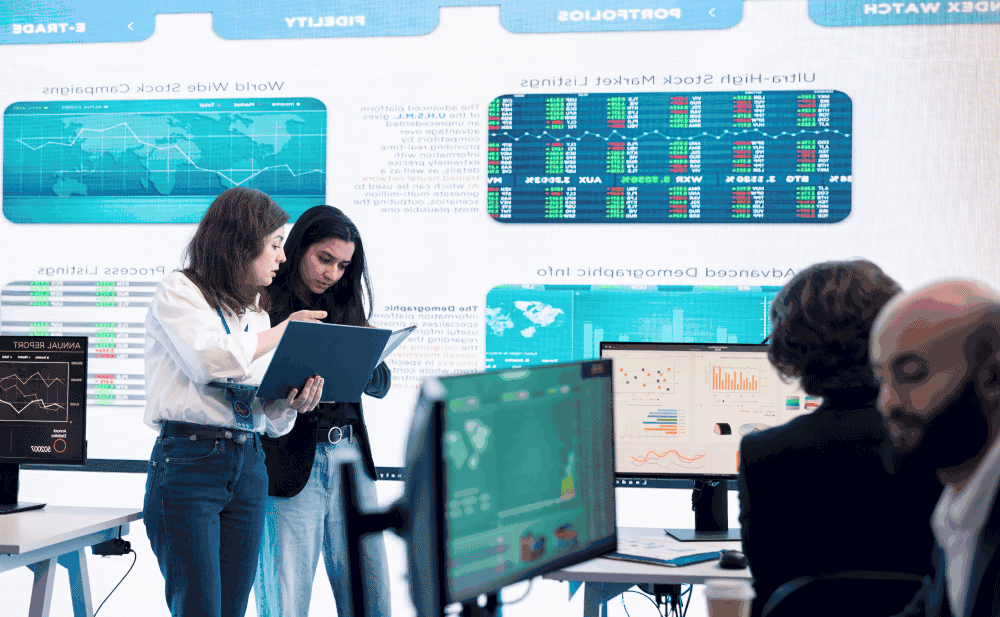
The Power of Secure Engineering Data Exchange
Success in the automotive supply chain requires speed, precision, and above all, security. Your engineering teams are constantly innovating, designing, and collaborating on complex projects that push boundaries. But are your current file-sharing practices empowering this innovation, or might they be creating bottlenecks and exposing your valuable intellectual property to unnecessary risks?
May 30, 2025
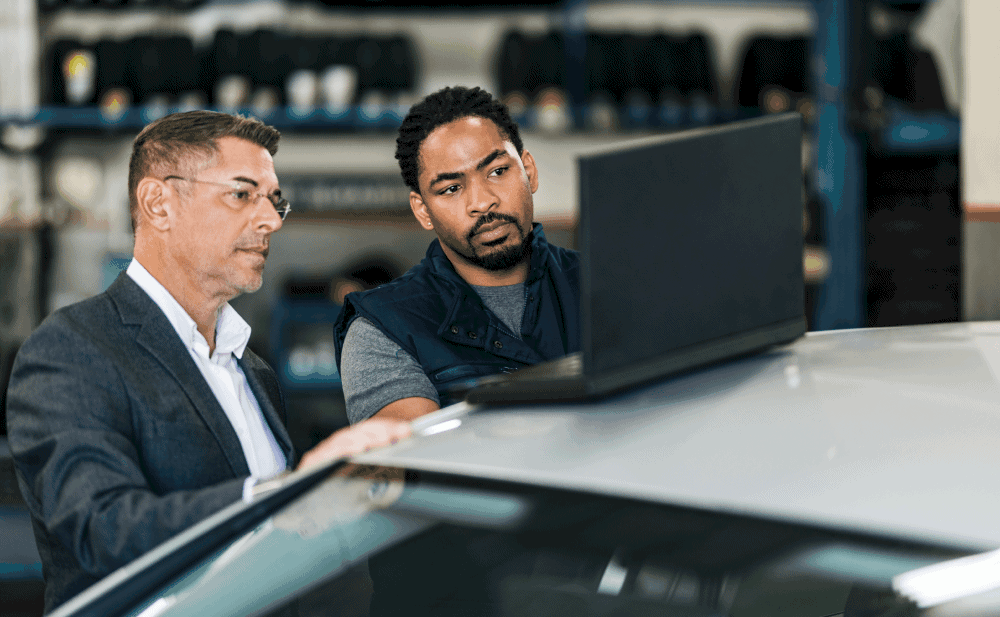
Solving Challenges in OEM-Supplier Data Exchange
OEM-supplier data exchange is a critical function, yet it's often a minefield of potential problems, with a serious impact if left unaddressed. Mistakes occurring anywhere in this highly complex process don't just cause minor hiccups; they can incur significant costs, lead to project delays, introduce production errors, and damage trust in commercial relationships.
May 30, 2025
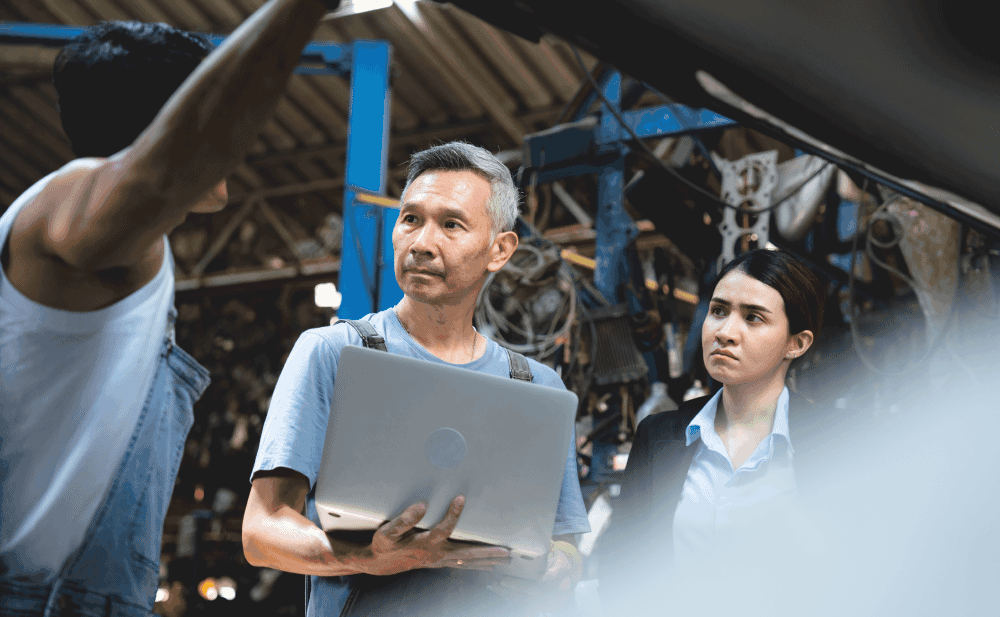
Mastering Automotive Data Exchange: OEM-Supplier Collaboration
Amid the rise of electrification, connected vehicles, and increasingly complex global supply chains, getting data exchange right isn't just beneficial; it's a commercial imperative. Efficient data exchange is crucial to product development, minimising costly delays, reducing time-to-market, and maintaining strong, productive partnerships.
May 30, 2025
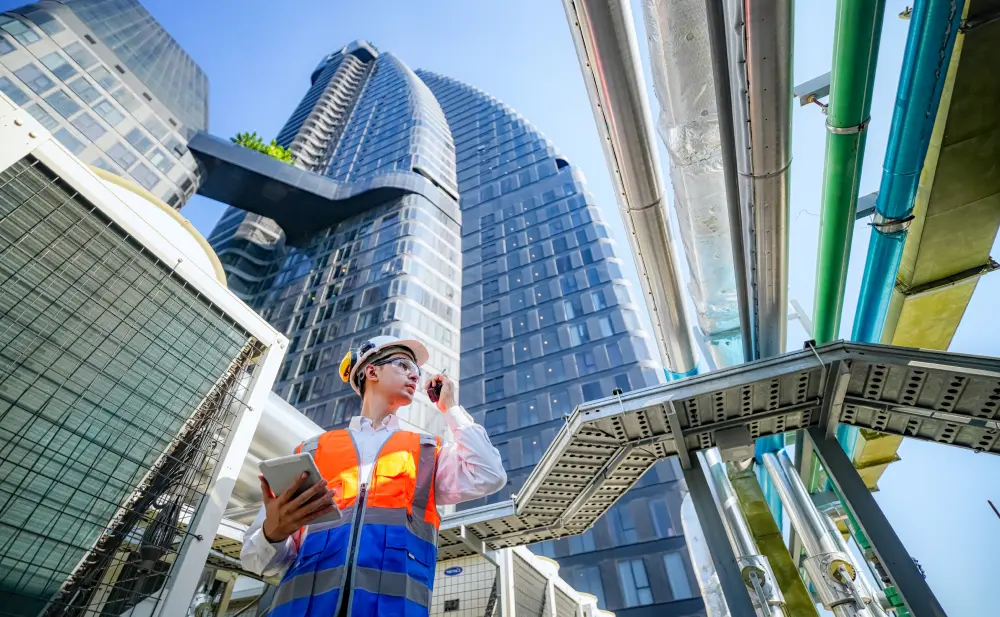
Navigating the complexity of Smart Building technology
The promise of intelligent buildings – responsive, efficient, user-friendly environments powered by smart technology and underpinned by Building Information Modelling (BIM) – is compelling. However, the path towards this digital transformation is rarely straightforward.
May 28, 2025
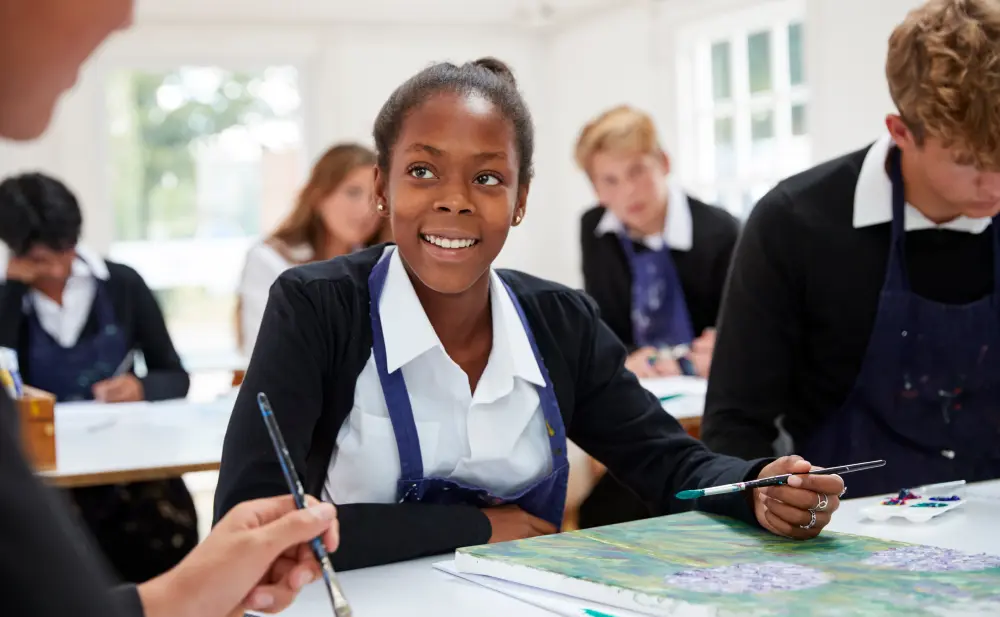
Setting the standard for DfE projects: 99% compliance
Majenta was recently awarded an exceptional compliance score – exceeding 99% – for our work on a significant Department for Education (DfE) project, representing one of the highest ratings ever achieved. Our Technical Director, James Smith, who oversaw the project, explains the significance of the achievement.
May 22, 2025
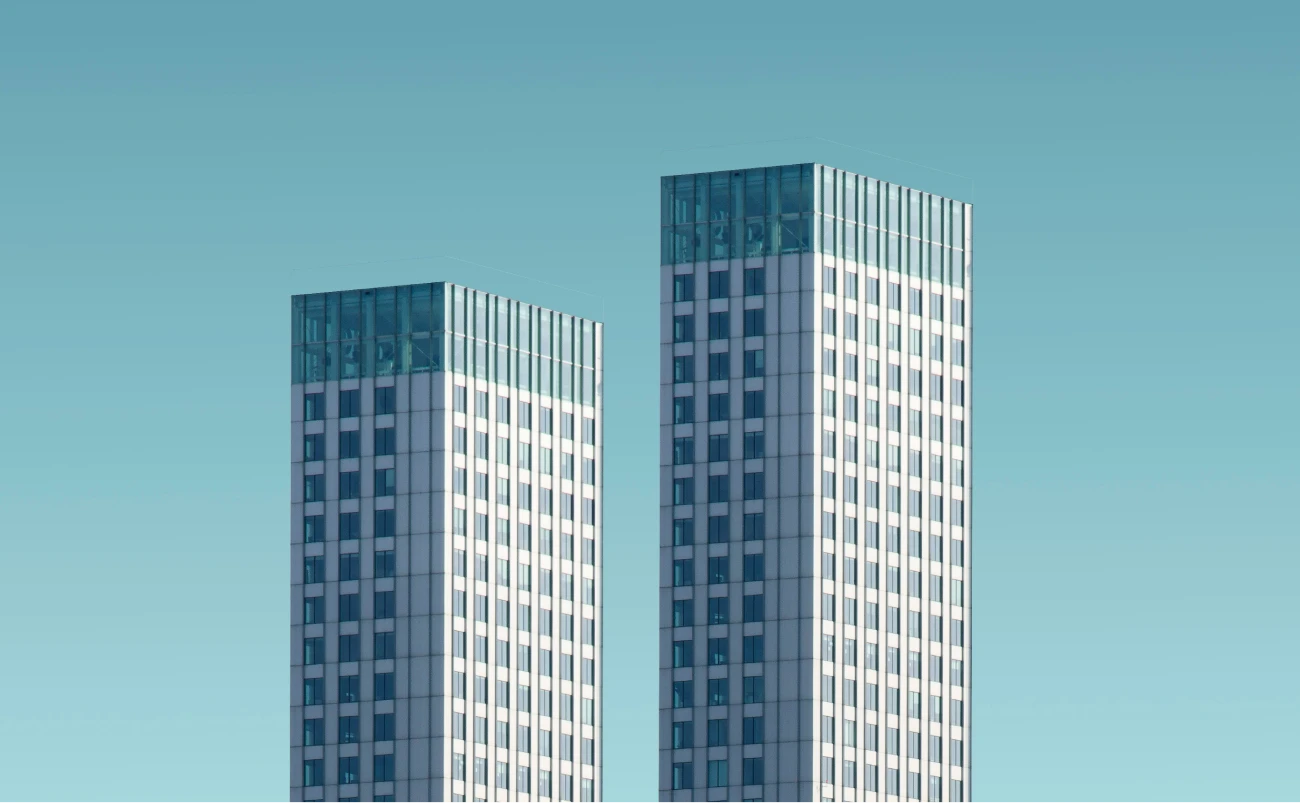
Unlock the potential of Smart Buildings with BIM
Managing large and complex building estates efficiently demands accurate, accessible, real-time data to optimise building performance, enhance the experience for occupants, and meet ever-more-pressing sustainability goals. The good news is that Building Information Modelling (BIM) and smart building technologies, when integrated effectively, can create truly “smart” buildings which meet these needs.
May 21, 2025
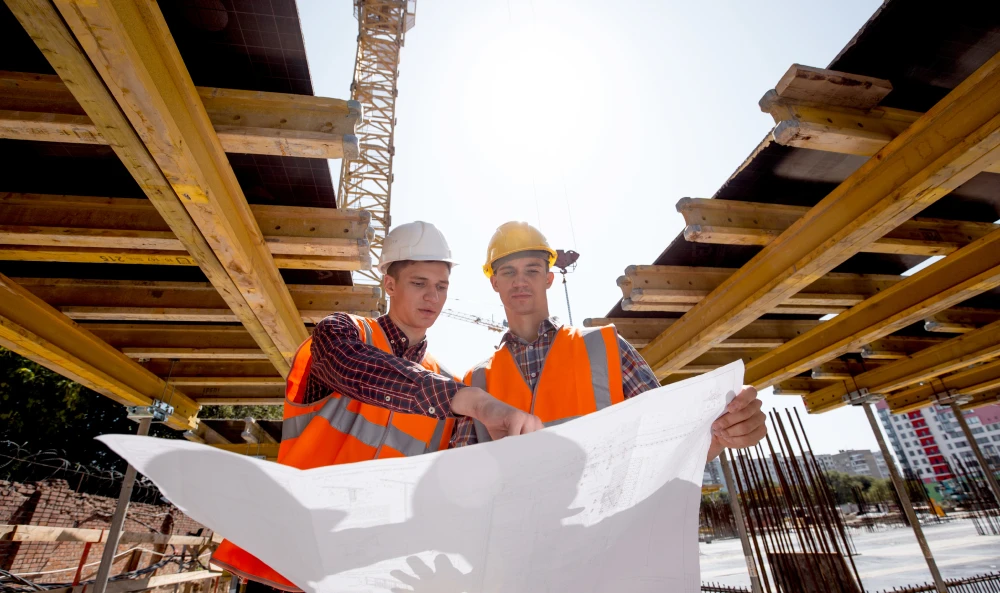
5 Common Challenges in ISO 19650 Implementation
The benefits of adopting ISO 19650 for managing information in construction and asset management are compelling – improved efficiency, reduced risk, better collaboration, and enhanced long-term value. However, as we’ve seen in many of the organisations we work with, the path towards successfully implementing this global standard isn't always clear. Recognising the common pain points is therefore a crucial first step towards developing effective strategies to address them.
May 12, 2025
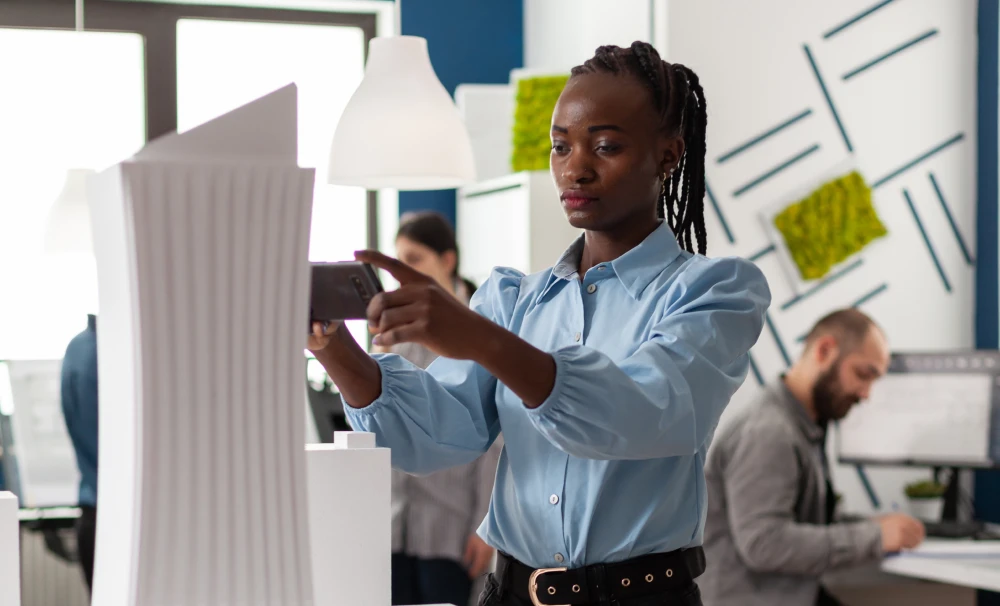
Debunking 4D modelling myths: overcoming common hurdles in construction
Adopting new technologies can feel like navigating uncharted territory, and understandably, misconceptions often arise. 4D modelling in construction is one such example. As specialists, we know it offers transformative potential for construction projects. But we’re also aware that some clients are hesitant to implement it — perhaps held back by misunderstandings about its utility, cost, or value add.
May 6, 2025
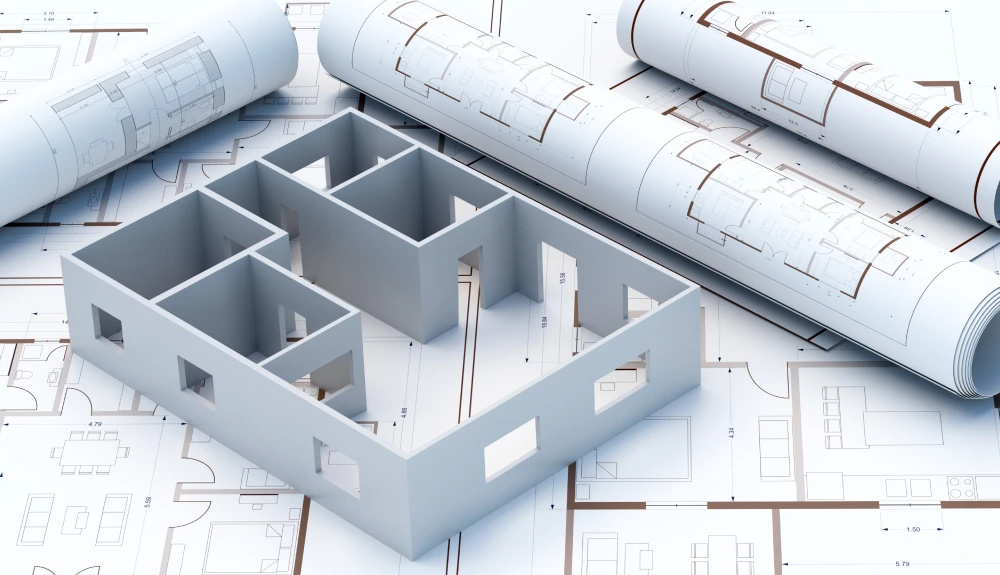
Unlock project success: Why 4D modelling is transformative for construction
Within the construction industry, evolving digital technologies are paving the way for smarter, safer, and more efficient projects. At the forefront is Majenta’s 4D modelling service – a new approach to project visualisation that integrates 3D design models with the crucial fourth dimension: time, by integrating key details from the project schedule.
May 6, 2025
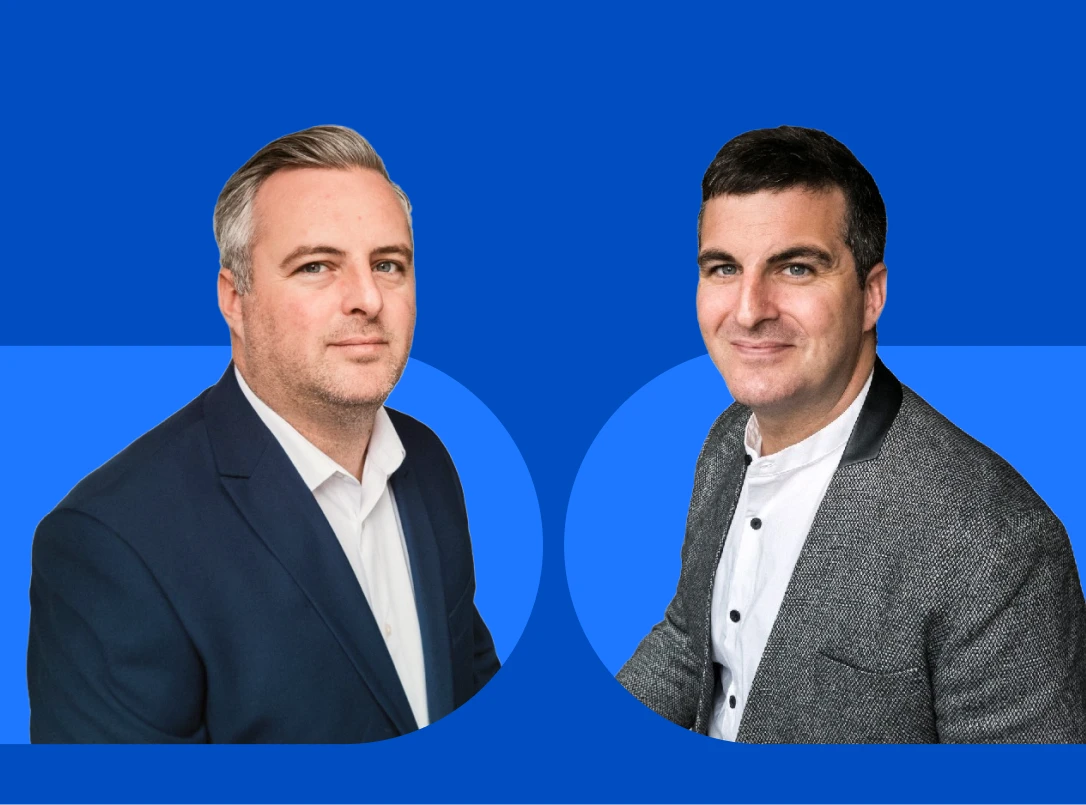
The Byrne Brothers — reflecting Majenta’s breadth of expertise
At Majenta, tackling complex challenges often involves bringing together diverse expertise. A perfect example of this synergy in action can be found within our automotive team: brothers Mike and Antony Byrne, who’ve been with Majenta for the past seven and eight years, respectively.
May 6, 2025
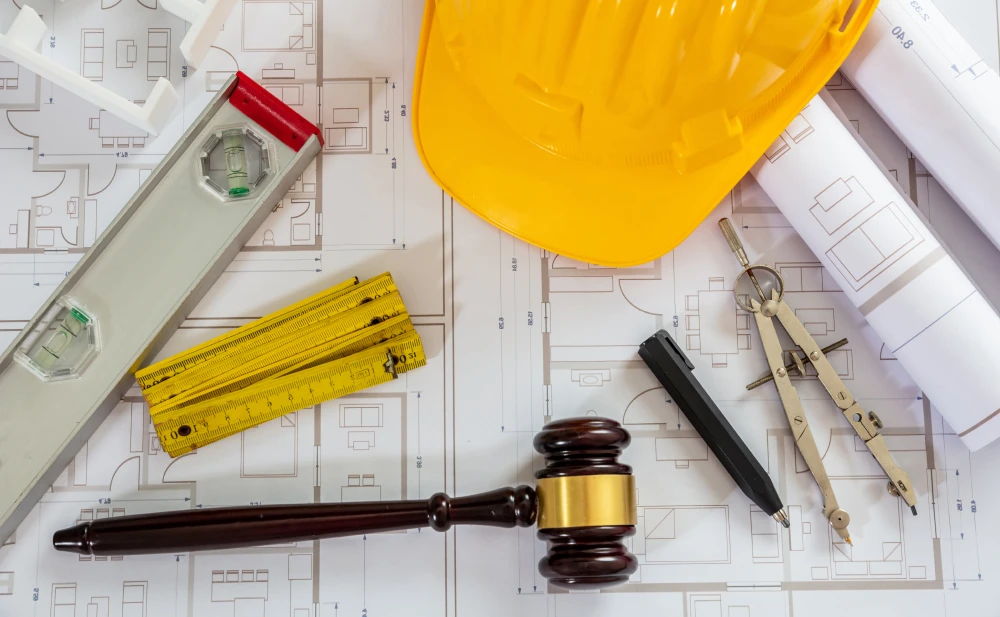
Overcoming Hurdles in Data Management and Compliance
The Building Safety Act (2022) mandates crucial reforms necessary to improve safety standards across the built environment. But for many construction industry organisations, fulfilling the comprehensive requirements laid out in the Act is far from straightforward.
May 6, 2025
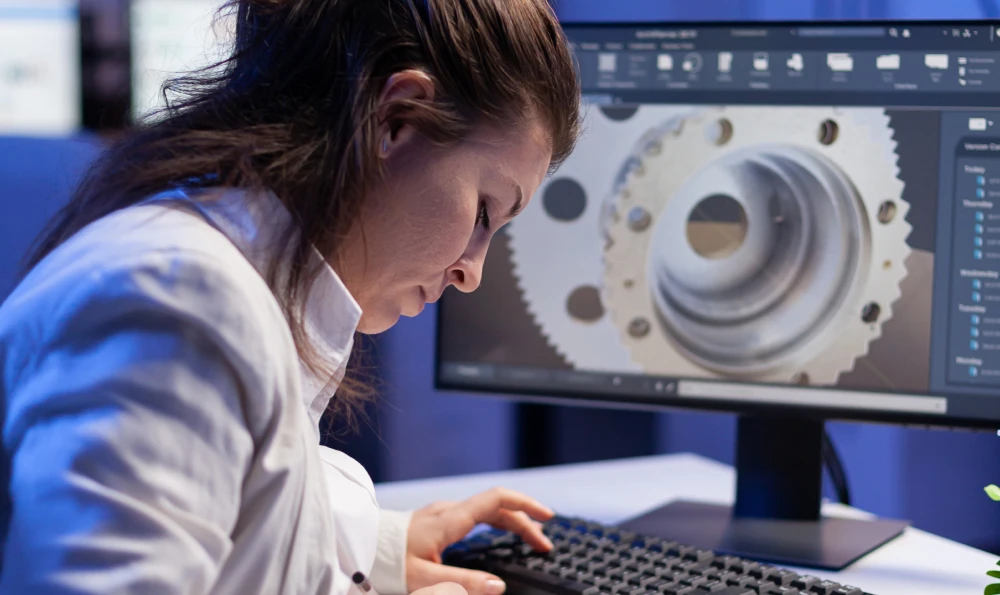
Hidden toll: Exposing the real cost of inefficient CAD data exchange
Developing modern vehicles is an increasingly complex undertaking, relying on a network of hundreds of suppliers providing thousands of individual parts, and underpinned by complex scheduling, logistics and communication requirements. But in many cases, beneath the surface, there’s a significant – and often greatly underestimated – drain on resources, time, and money. We’re talking about inefficient CAD data exchange.
May 6, 2025
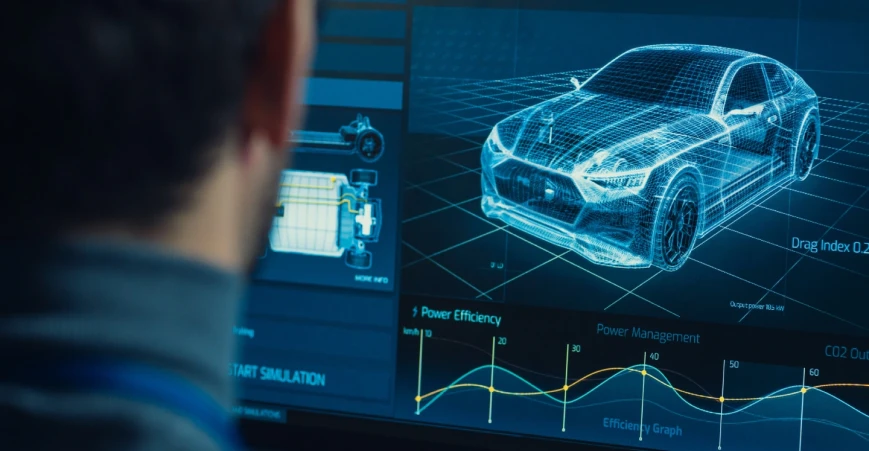
The competitive advantage of efficient CAD data exchange
The modern automotive supply chain relies on a delicate balance of logistics, communication and timing. A typical vehicle program can involve around 300 suppliers contributing over 30,000 parts, with suppliers themselves designing and engineering more than 60% of these components.
May 6, 2025
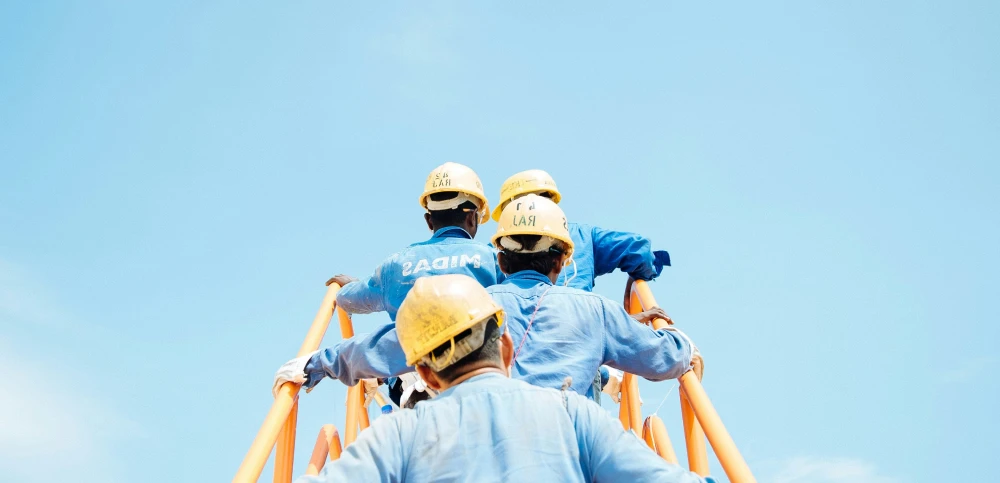
How Robust Information Management Creates Safer, More Compliant Buildings
Two central pillars of the Building Safety Act for HRBs are the 'golden thread' of information and the mandatory gateway points, and effective information management is fundamental to successfully addressing both.
May 6, 2025
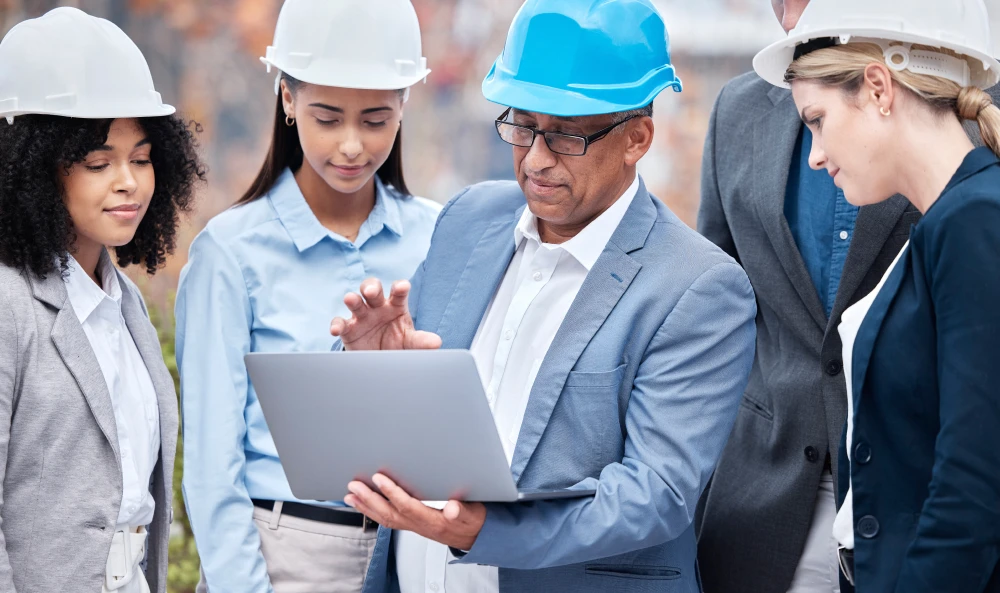
How ISO 19650 Information Management Drives Project Success
In the modern construction sector, effectively managing information is critical for efficiency, safety, compliance and long-term success. But whether you're dealing with buildings, infrastructure, or utilities, the sheer volume of data generated throughout an asset's lifecycle can be overwhelming.
May 5, 2025
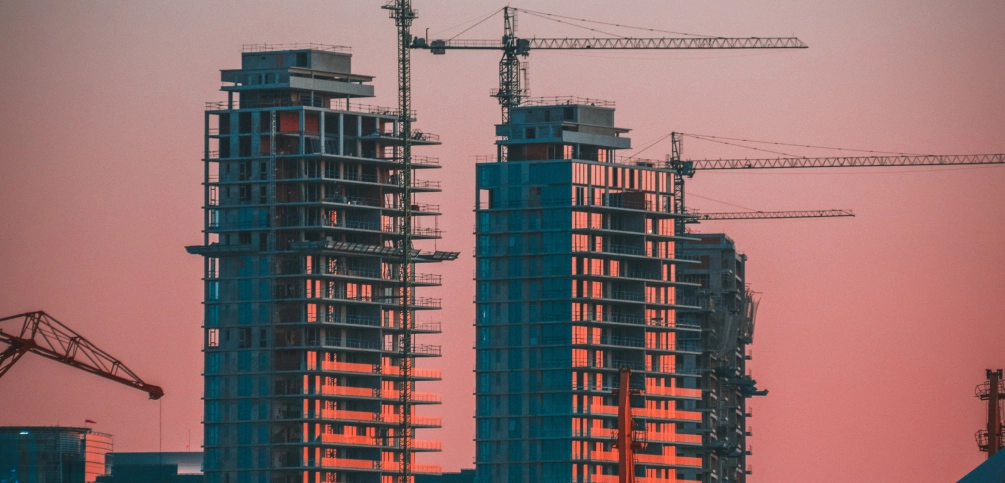
Unlocking Efficiency: The Power of Information
In an era where technology is transforming industries at an unprecedented pace...
June 24, 2024
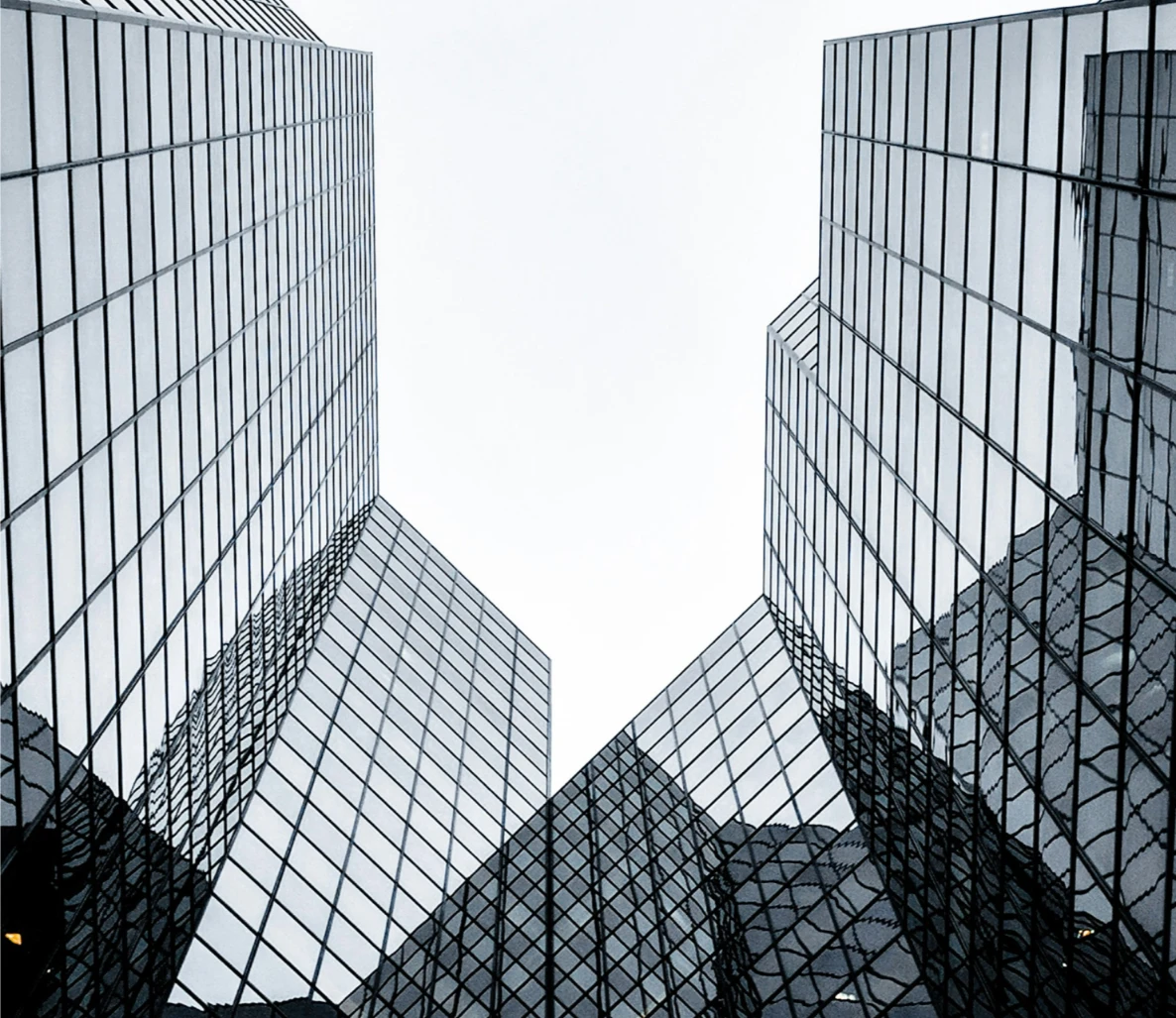
Elements of an Effective Meeting
A successful meeting is well-structured, purposeful, and efficiently achieves its intended outcomes...
June 24, 2024
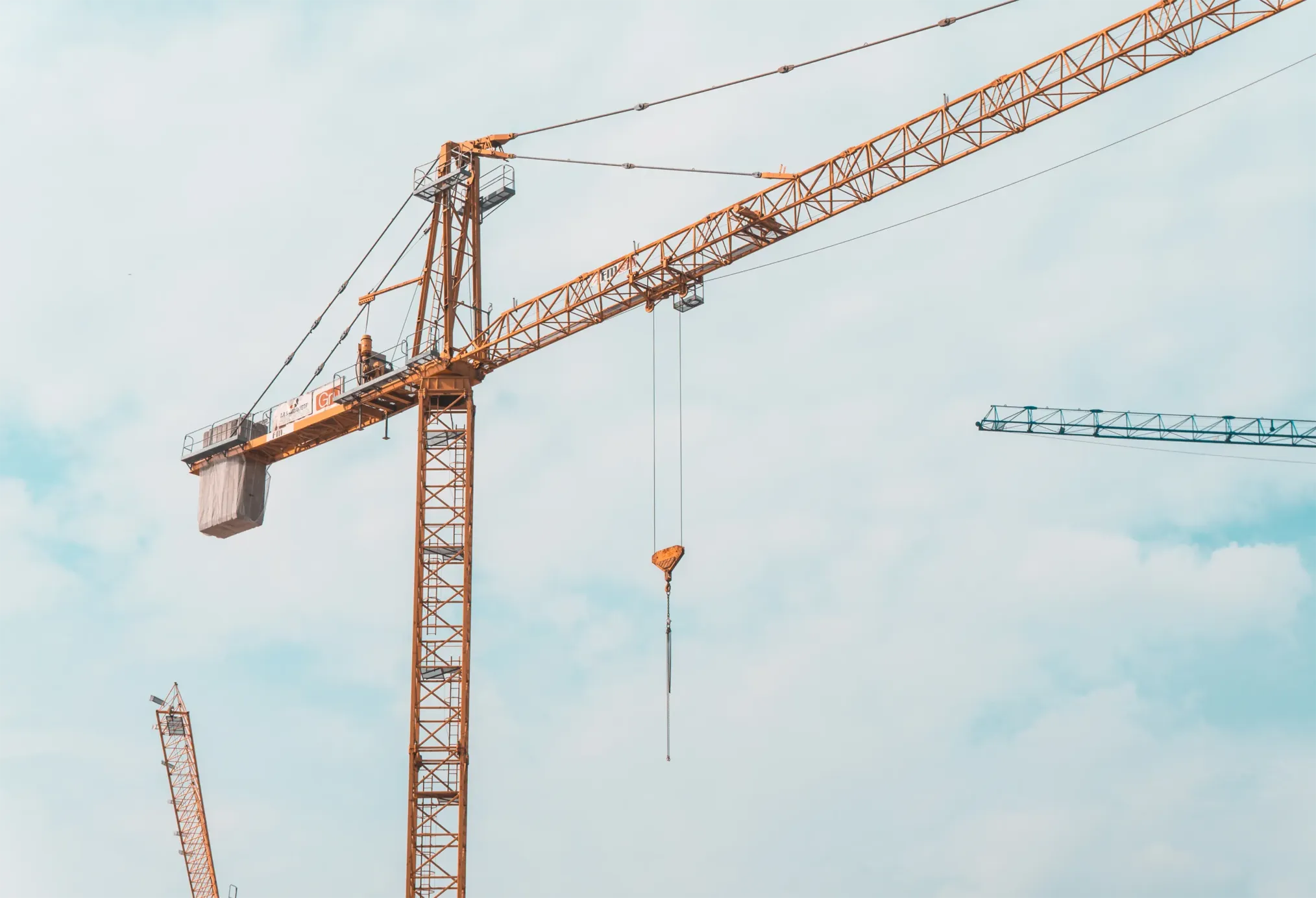
Pros & Cons of Parametric Revit Families – and When to Use Them
In the architecture, engineering, and construction (AEC) industry, high-quality Building Information Modeling (BIM)...
November 10, 2023